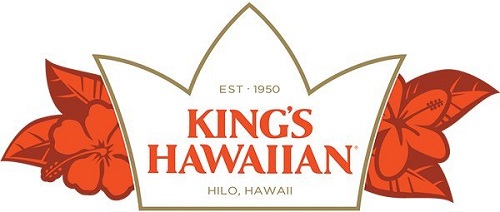
Unlock the Secrets to Increased Productivity with Redzone's Newly Released Benchmark Report! Download Today
Customers / Industries / Baked Goods
For bakeries, delays in production are no small matter. If left to sit for too long, perishable ingredients and goods run the risk of spoilage, leading to lost profits, reduced quality, and food safety concerns. In order to prevent that from happening, plants need to operate at maximum efficiency.
QAD Redzone’s bakery management software empowers your frontline workers with the tools and technology they need to prevent unexpected downtime, stay productive, and deliver products that are as high quality as they are delicious.
Boost your competitive standing by significantly increasing productivity in just 90 days, enabling you to overcome tight margins and become the lowest-cost producer.
Improve equipment reliability and keep volumes on your long lines high by activating operator care across your facility.
Dramatically shorten changeovers and other planned downtime to reduce spoilage risks for materials that are sensitive to environmental inconsistencies.
Become more action-oriented with action management and kaizen events to eliminate frustrating issues that continuously drain your productivity.
Maintain detailed records of current and new product recipes, including versions, revisions and batch history notes, all in one place.
More easily manage expensive raw materials with statistical process control (SPC) and out-of-the-box analytics to reduce waste and giveaway for baked goods.
Comply with changing food safety regulations and packaging requirements by digitizing paper-based processes for quicker, more impactful audits.
Minimize IT burden and environmental risks with secure cloud technology and off-the-shelf automation.
Ensure the highest quality throughout every step of the manufacturing process with plant-wide quality dashboards and detailed digital records.
Trace raw materials and the flow of product throughout your facility to ensure quality and improve allergen segregation and management.
Every other year, we conduct a benchmark study against the QAD Redzone 90-day productivity program to assess the effectiveness of the QAD Redzone Connect Workforce Solution. This study compares baseline OEE to the resulting OEE uplift after 90 days and calculates the productivity improvement.
All of QAD Redzone’s community members see OEE uplifts in 90 days — sophisticated, global manufacturers can expect double-digit increases, while smaller, less mature plants see OEE uplifts of >30%.
With an average OEE uplift of 12% and an associated 22% productivity improvement across the entire sample, users enjoy additional capacity without adding resources and can reduce costs without increasing output.
Perhaps the most impactful outcome of this study is the cultural phenomenon that results from improved communication across all plants considered.
See what results manufacturers have achieved using our bakery management software:
Our bakery management software helps manufacturers achieve sustainable and organic double-digit productivity improvements to increase revenue and margins, all without adding people or equipment.
Our solution enables plants to motivate frontline workers through on-the-job learning opportunities and real-time communications, dramatically reducing turnover and transforming a disengaged workforce into a collaborative, connected team that’s energized to excel. With QAD Redzone on your side, you’ll be able to create a lean manufacturing culture that embraces continuous improvement, all driven by shop floor ownership.
Get the full story behind how food manufacturing titan Post Holdings enhanced productivity, engagement and growth by 12% across 36 manufacturing plants with help from QAD Redzone.
Discover how QAD Redzone’s bakery management software helps Empire Bakery Commissary connect its workforce and gives frontline workers the tools they need to succeed, all while baking incredible cakes for its customers.
Find out how Companion Baking Co. was able to achieve significant OEE uplift and productivity improvements in this plant tour.
Hear how Companion Baking Co. and other QAD Redzone community members elevate employee onboarding and lower turnover using our bakery software.
We understand that bakery manufacturing is a complex industry that requires many different software solutions to manage the various aspects of the production process. Our bakery management software solution features integrations with various systems, including:
By integrating our bakery management software solutions within these systems, we enable you to streamline operations, reducing waste and downtime, which helps to lower costs and increase revenue.
Discover how plants authentically transformed their level of frontline engagement.
Contact us and let's begin empowering your frontline and growing your bottomline.