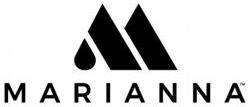
Découvrez les histoires inspirantes des travailleurs de première ligne : les grands noms de l’industrie manufacturière ! En savoir plus
Nous comprenons qu’il est difficile de gérer l’imprévisible. Des choses se produisent. Mais lorsque les opérateurs, le contrôle de la qualité et la maintenance travaillent ensemble, les impacts négatifs peuvent être réduits et les soins préventifs globaux peuvent conduire à des machines « bien huilées » et à des résultats plus prévisibles.
Réduisez considérablement les temps d’arrêt non planifiés en incitant les opérateurs à entretenir leur équipement afin de détecter les problèmes plus tôt et de libérer l’équipe de maintenance pour qu’elle se concentre sur l’entretien préventif.
Avec la maintenance productive totale (TPM) dans une boîte, transférez l’entretien des équipements aux opérateurs et éliminez la tension entre la production et la maintenance – il y a même un « téléphone chauve-souris » pour les cas où les choses tournent mal.
Le module Redzone Reliability étend la solution Redzone Connected Workforce à votre service de maintenance – fonctionnant comme un puissant logiciel de GMAO – afin d’accroître encore la valeur de l’amélioration continue de la productivité.
En fournissant des outils spécifiques à la maintenance pour mieux gérer les ordres de travail, l’équipe de maintenance peut consacrer plus de temps à la maintenance préventive (PM), mais lorsqu’elle est associée à un nouveau niveau de connexion avec la production, le tout est plus grand que la somme de ses parties, avec des opérateurs effectuant des tâches de maintenance de base. Ces capacités correspondent à ce que vous attendez d’un logiciel de GMAO de premier plan, aidant les équipes de maintenance à se concentrer davantage sur la prévention et moins sur les réparations réactives.
Le module Redzone Reliability élargit la portée de votre équipe en activant les sens de la vue, du son et de l’odorat des opérateurs afin d’identifier les problèmes potentiels avant qu’ils n’entraînent des temps d’arrêt perturbateurs. Lorsque l’inévitable événement imprévu se produit, la communication instantanée minimise son impact.
L’entretien des équipements n’est plus seulement une responsabilité de maintenance. Avec Redzone, les usines transfèrent les tâches de nettoyage, d’inspection et de lubrification (CIL) aux opérateurs. En fin de compte, les opérateurs acquièrent de nouvelles compétences, les techniciens de maintenance sont libérés et les temps d’arrêt non planifiés sont évités. Les lignes centrales numériques garantissent une seule et même façon de configurer et d’exploiter la ligne.
Développez vos ressources de maintenance en intégrant des opérateurs dans l’équipe.
Supprimez la barrière entre la production et la maintenance grâce aux rapports sur l’état de l’équipement. Le rapport de santé permet à la production et à la maintenance d’approfondir les éléments clés de la fiabilité, notamment la détection précoce des défauts (sens de l’opérateur), les demandes de service, les pannes, les CIL et les PM. Les interactions favorisent l’amélioration des compétences des employés de production en ce qui concerne l’entretien de leur équipement.
Bien que la prévention soit essentielle, l’imprévu se produit inévitablement. Les opérateurs appellent les techniciens en utilisant « Uber pour la maintenance » pour s’assurer que la bonne information parvient immédiatement à la bonne personne afin de minimiser les temps d’arrêt. Pour la première fois, les usines savent exactement quand une ligne s’est arrêtée, quand l’aide a été demandée, quand l’aide est arrivée et quand la ligne a été remise en service.
Les pannes surviennent. Réduisez leur impact.
Le module Fiabilité complète la connexion entre les équipes de production, de qualité et de maintenance, afin de minimiser les perturbations et les temps d’arrêt non planifiés dans l’atelier. Lorsque tout le monde travaille à partir de la même solution de main-d’œuvre connectée, la collaboration de l’ensemble de l’équipe des opérations est renforcée, et davantage de problèmes sont identifiés et corrigés plus tôt et de manière proactive, car tout le monde se concentre sur les mêmes objectifs. Ce type d’alignement de l’équipe est au cœur de ce qu’un logiciel de GMAO moderne devrait faciliter : connecter les personnes, les processus et les priorités en temps réel.
Résultats typiques :
Mis en œuvre dans plus de 1 500 usines à travers le monde, il a un impact transformateur sur les personnes, les équipes et votre entreprise. Vos collaborateurs apprennent par la pratique ; ainsi, même les personnes les plus timides sur le plan technique deviendront des experts en un rien de temps.
Contactez-nous et commençons à responsabiliser votre personnel de première ligne et à augmenter vos bénéfices.