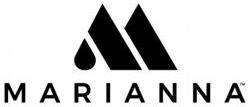
Descubre las inspiradoras historias de los Rostros de la primera línea: ¡Las estrellas de la fabricación! Leer más
Entendemos que gestionar lo imprevisible es difícil. Las cosas ocurren. Pero cuando los operarios, el control de calidad y el mantenimiento trabajan juntos, los impactos negativos pueden reducirse y el cuidado preventivo general puede conducir a máquinas «bien engrasadas» y resultados más predecibles.
Reduce significativamente los tiempos de inactividad imprevistos implicando a los operarios en el mantenimiento de sus equipos para detectar antes los problemas y liberar al equipo de Mantenimiento para que se centre en el mantenimiento preventivo.
Con el Mantenimiento Productivo Total (TPM) en una caja, transfiere el cuidado de los equipos a los operarios y elimina la tensión entre producción y mantenimiento; incluso hay un «bat-teléfono» para cuando las cosas van mal.
El módulo Redzone Fiabilidad amplía la solución Redzone Connected Workforce a tu departamento de Mantenimiento -funcionando como un potente software GMAO- para extender aún más el valor de la mejora continua de la productividad.
Al ofrecer herramientas específicas de mantenimiento para gestionar mejor las órdenes de trabajo de mantenimiento periódico, el equipo de Mantenimiento puede dedicar más tiempo al mantenimiento preventivo (MP), pero cuando se combina con un nuevo nivel de conexión con la producción, el todo es mayor que la suma de sus partes; con operarios que realizan tareas básicas de mantenimiento. Estas funciones se ajustan a lo que cabría esperar de un software de GMAO líder, ayudando a los equipos de mantenimiento a centrarse más en la prevención y menos en las reparaciones reactivas.
El módulo de Fiabilidad Redzone amplía el alcance de tu equipo activando el sentido de la vista, el oído y el olfato de los operarios para identificar posibles problemas antes de que provoquen un tiempo de inactividad perjudicial. Cuando se produce el inevitable imprevisto, la comunicación instantánea minimiza su impacto.
El cuidado de los equipos ya no es sólo responsabilidad del mantenimiento. Con Redzone, las fábricas transfieren las tareas de limpieza, inspección y lubricación (CIL) a los operarios: en última instancia, se mejora la cualificación de los operarios, se libera a los técnicos de mantenimiento y se evitan paradas imprevistas. Las líneas centrales digitales garantizan una forma correcta de configurar y hacer funcionar la línea.
Amplía tus recursos de mantenimiento incluyendo operarios en el equipo.
Elimina la barrera entre producción y mantenimiento con los informes de salud de los equipos. El informe de salud permite a producción y mantenimiento profundizar en elementos clave de fiabilidad, como la detección precoz de defectos (sentidos del operario), las solicitudes de servicio, las averías, los CIL y los PM. Las interacciones promueven la capacitación de los empleados de producción en el cuidado de sus equipos.
Aunque la prevención es clave, lo imprevisto ocurre inevitablemente. Los operarios llaman a los técnicos utilizando «Uber para mantenimiento» para asegurarse de que la información correcta llega inmediatamente a la persona adecuada para minimizar el tiempo de inactividad. Por primera vez, las plantas saben exactamente cuándo se detuvo una línea, cuándo se solicitó ayuda, cuándo llegó la ayuda y cuándo la línea volvió a funcionar.
Las averías ocurren. Reduce su impacto.
El módulo de Fiabilidad completa la conexión entre el equipo de equipos de Producción, Calidad y Mantenimiento, para minimizar las interrupciones no planificadas y el tiempo de inactividad en el taller. Con todos trabajando desde la misma solución de fuerza de trabajo conectada, se eleva la colaboración de todo el equipo de Operaciones, y se identifican y corrigen más problemas antes y de forma proactiva, porque todos se centran en los mismos objetivos. Este tipo de alineación del equipo es fundamental para lo que debe facilitar un software de GMAO moderno: conectar personas, procesos y prioridades en tiempo real.
Resultados típicos:
Implantado en más de 1500 fábricas de todo el mundo, el impacto en las personas, los equipos y tu empresa es transformador. Tu gente aprende haciendo, así que hasta los más tímidos en tecnología se convertirán en expertos en poco tiempo.
Ponte en contacto con nosotros y comencemos a empoderar a tu primera línea y a aumentar tus ganancias.